“쿵, 쿵, 쿵!”
지난달 12일 경기 광명시 ‘기아 오토랜드 광명’ 프레스공장에 들어서자 규칙적으로 굉음이 울리며 묵직한 진동이 전해졌다. 프레스 기계가 카니발과 EV9의 외판을 찍어내는 작업이 한창이었다. 두께 0.7T(㎜)의 납작한 철판이 프레스 기계를 거쳐 차체의 외형으로 거듭나는 순간 프레스 라인 아래에서는 또 다른 공정이 진행되고 있었다. 외판 가공 과정에서 나온 철 부스러기인 ‘철 스크랩’을 모아서 재활용하는 작업이다.
기업의 탄소중립이 중요한 과제로 떠오르며 기아는 철 스크랩 등을 이용해 적극적으로 자원재순환을 확대하고 있다. 전동화 시대를 맞아 자동차 공장이 전기차를 포함한 미래 모빌리티 생산기지로 거듭나며 탄소중립 활동은 더욱 활발해질 전망이다.
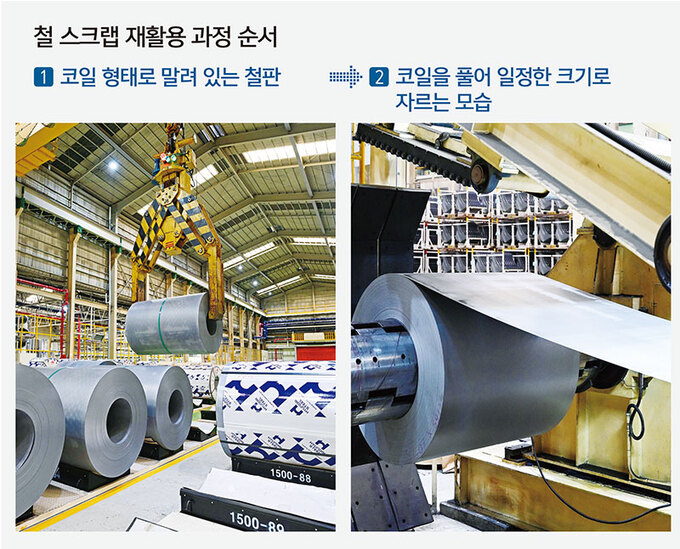
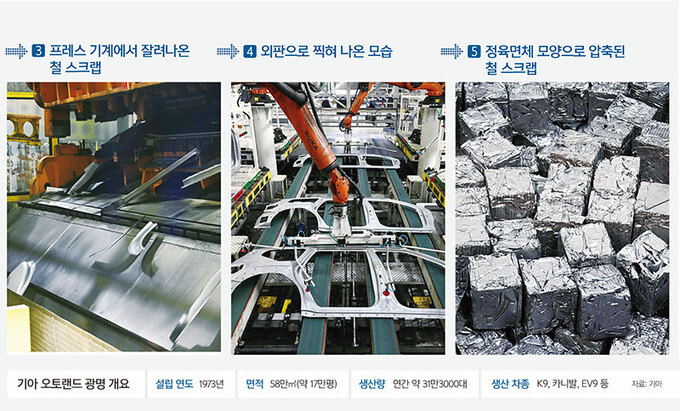
◆철 스크랩으로 자원재순환
이날 언론에 처음 공개된 기아 오토랜드 광명의 프레스공장은 자동차 생산의 첫 단계인 외판을 찍어내는 곳이다.
철강사(현대제철)에서 온 철판은 마치 두루마리 휴지처럼 말려 있는 코일의 형태로, 10t 이상 무게가 나간다. 코일을 풀어 차종의 형태나 크기에 맞게 일정한 크기로 잘린 철판이 프레스 기계로 옮겨졌다. 철판은 카니발과 EV9의 금형이 장착된 고압 프레스 기계에 한 장씩 들어가 후드, 루프, 펜더 등의 외판으로 찍혀 나왔다.
이 과정에서 수집된 철 스크랩은 컨베이어벨트를 타고 베일 프레스로 이동해 한 변이 30㎝인 정육면체 형태로 압축된다. 압축을 하면 운송효율이 150% 높아져 운송비가 절감되고, 생산성 향상 효과도 있다. 이들 철 스크랩은 다시 철강사로 이동해 다시 자동차용 코일로 재생산되거나 자동차 부품으로 재탄생된다.
과거 그냥 버려졌던 철 스크랩은 원자재값이 오르며 이제 ‘귀한 몸’ 대접을 받고 있다. 특히 수입에 의존하는 다른 철강 자원과 달리 철 스크랩은 국내 공급이 70∼80% 수준이어서 환경 부담을 줄이는 데 큰 역할을 하고 있다.
기아 공장에서 발생하는 7만3000t의 스크랩을 재활용해 연간 약 16만t의 이산화탄소 배출 감축 효과를 내고 있다. 제철소에 매각된 스크랩 금액은 지난해 기준 478억원이다.
철 스크랩 외에도 자동차 생산 과정에서 탄소 배출을 줄이기 위한 섬세한 공정이 더해진다.
일정한 크기로 잘라진 철판을 쌓아 보관할 때 보관장의 청결을 유지하고 손상을 방지해 과거와 달리 모든 철판을 사용할 수 있게 됐다. 또한 버려지는 스크랩의 양을 최소화하기 위해 정확한 크기를 도출하고 제품을 생산하는 금형 구조를 최적화한다. 각각 연간 245t, 1220t의 탄소 배출량 절감 효과가 있다.
◆국내 첫 전기차 전용 공장… 순환경제 가속
오토랜드 광명은 올해 국내 첫 전기차 전용 공장으로 전환되며 이러한 친환경 활동을 더욱 가속할 예정이다. 1973년 국내 첫 컨베이어벨트로 생산되는 일관(一貫)공정 종합 자동차 공장으로 설립된 이 공장이 50여년 만에 또다시 큰 변화를 맞게 되는 것이다.
올해 초 현대차그룹은 전동화 의지를 나타내기 위해 이례적으로 오토랜드 광명에서 신년회를 열었다.
정의선 현대차그룹 회장은 이 자리에서 “이곳에서 출발해 울산과 미국, 글로벌로 이어지게 될 전동화의 혁신이 진심으로 기대된다”고 밝혔다.
현대차그룹은 2분기에 광명 전기차 전용공장을 완공하고 소형 전기차 EV3를 생산해 국내외에 판매할 계획이다. 이후 미국 현대차그룹 메타플랜트 아메리카, 기아 오토랜드 화성 전기차 전용공장, 현대차 울산 전기차 전용공장을 순차적으로 가동해 2030년 전기차 글로벌 톱3로 자리매김한다는 전략이다.
정 회장은 환경을 위한 사회적 책임도 강조했다.
그는 “인류와 함께 지속성장하기 위해 탄소중립과 순환경제에 더욱 관심을 가져야 한다”며 “이를 위해 수소 생태계를 신속히 조성하고 전기차 배터리를 비롯한 자원 재활용 등 순환경제를 활성화해 글로벌 기업으로서 사회적 책임에 앞장서 나가야 한다”고 말했다.